Phone: 218-481-3500
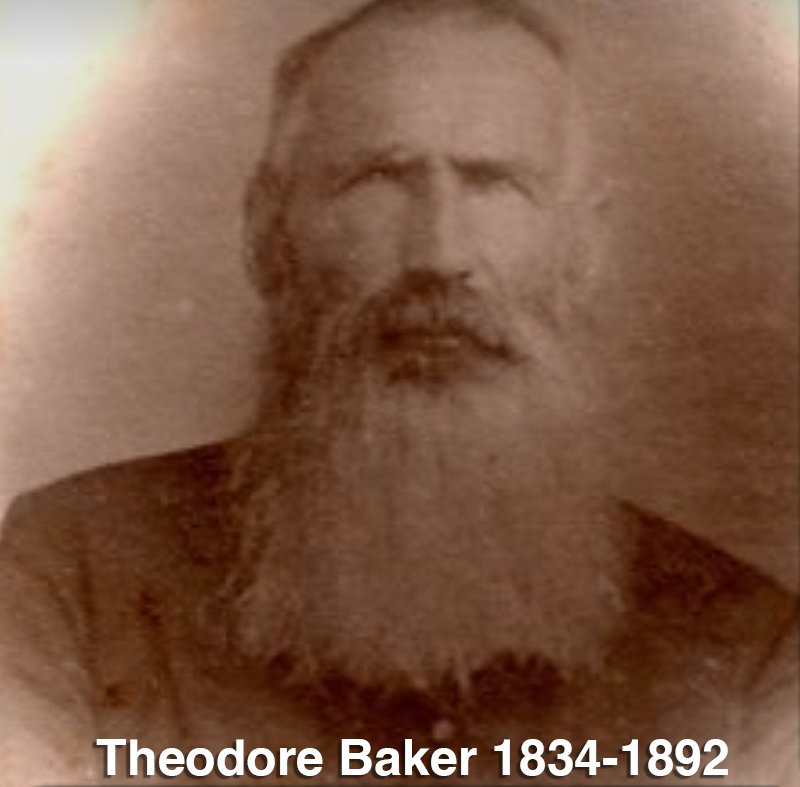
Company Values
Expertise & Excellence
Committed to delivering top-tier solutions with precision, efficiency, and the highest industry standards.
Problem-Solving
We thrive on tackling complex challenges with creative, forward-thinking solutions.
Continuity, Accountability & Transparency
The organization ensured the continuity of its mission by maintaining clear accountability among its team members while promoting transparency in all its operations.
Customer-Centric Approach
Your success is our priority; we build lasting partnerships through trust, quality, and exceptional service.
Expertise in These Areas
With years of hands-on experience and a commitment to excellence, we provide industry-leading expertise in installation, Startup & commissioning, project management, and repair of advanced systems.
Pneumatic Conveying Systems
- Dilute Phase: Materials are suspended in the air stream and carried at high velocities, which is suitable for lighter materials over longer distances through the pipe.
- Dense Phase: Materials move in a slug or plug form at lower velocities, which is ideal for heavy or fragile materials to prevent damage.
Depending on the material and distance involved, these systems can be tailored to various needs. It’s a clean, flexible, and efficient method for material handling!
J.E. Baker Field Service will ensure your conveying system is installed and operating at peak performance.
Installation of Process Equipment
Installing equipment like extruders, loss-in-weight feeders, rotary feeders, screw conveyors, and diverter valves requires careful planning and execution to ensure efficiency and safety. Here are the general steps involved:
The process includes planning and site assessment, readiness and setup, implementation and installation, verification and calibration, and instruction and documentation.
Startup and Commissioning
Startup and commissioning refer to the final stages in the installation and preparation of equipment or systems, ensuring they are ready for operation. Here’s a breakdown:
The initial operation of equipment post-installation verifies that all components function as intended under normal conditions by powering on, conducting preliminary tests, and ensuring utilities are properly connected and operational while commissioning ensures a system operates safely, efficiently, and as designed by involving testing, adjustments, validations, safety inspections, performance fine-tuning, regulatory compliance, operator training, thorough documentation, formal handover to the owner, and requires meticulous attention to detail and systematic execution through comprehensive planning, complete documentation and procedures, pre-startup checks, collaborative teamwork, thorough testing, training and knowledge transfer, data collection and analysis, safety and compliance, contingency planning, and proper handover and support.
By adopting these best practices, you can minimize delays, reduce risks, and ensure a successful startup and commissioning. If you’re preparing for a specific project, I’d be happy to help refine these steps to suit your needs!